6 Things You Need to Know About Pole Barn Renovations
June 30, 2021
Pole barns are made to last. If built right, they can be perfectly serviceable for 50 years and more. Sometimes, though, weather happens – like hail. Or the owner outgrows the space that served so well for so long.
When it’s time for a barn renovation, from re-siding and re-roofing to adding additional square footage like a lean-to or even an office or warehouse space, there are a few things owners should know before they get started. To help, we talked with two of Lester Building’s renovation experts, territory managers Ron Knapper and Joe Bjelland. Here’s their advice:
“If you’re just replacing the steel siding, the initial consultation doesn’t have to be too involved,” Knapper explained. “But some customers want to reuse the existing steel, which makes sense economically. Unfortunately, it’s not always possible. If the steel is nailed on, it’ll be damaged when it’s taken off. If it’s screwed in, though, it will come off much cleaner and can be reused.”
Putting an addition on an existing structure is another story. “Make sure the renovation plans are reviewed by an engineer,” Bjelland said. “You need to understand what that building was initially designed for. If, for example, it was designed as an animal facility and the owner wants to turn it into a commercial building, that may or may not be possible based on the original plans.”
An engineer can also weigh in on whether a renovation will change snow drift loads on the roof, which can result in compromises to the building’s structural integrity. “Adding a taller addition to the end of a building could create an area on the roof of the existing building where snow accumulates,” Bjelland explained. “That snow drift load needs to be accounted for in renovation plans.”
“It’s not uncommon today for a customer to be disappointed after they commit to a project and then apply for permits,” Bjelland said. “The permitting process can take a long time and, by the time they’re approved, the materials prices will have changed dramatically – sometimes to the point where the customer has to put the project on hold so they can reconfigure their budget. Having said that, though, post frame construction is still an economical way to go because it typically requires less lumber than a traditional stick built structure.”
Reskinning can also reveal the unexpected – once the side panels are removed, you could discover that columns need replacing, too.
“Depending on the age of the building, you need to assess the condition of the columns,” Knapper said. “Periodically, a column will be rotted and we’ll have to stop what we’re doing, dig it out, and put in a new footing and column. I had a situation where the customer’s existing building was leaning well over a foot because the original builder didn’t put in the proper footings. Frost was getting to it and raising the structure. The only solution was to dig the columns out, put in bigger footings and reset the columns.”
The best way to prepare for unforeseen situations is to have a dedicated contingency budget. How much depends on the project, Bjelland said. “If you’re adding on to a building that has insulation and interior walls covering up the structure on the inside, you’re going to want more contingency money than if everything is open on the inside and you can clearly see the structure.”
“What type of renovation is possible depends on how the existing building was constructed,” Knapper said. “If your pole barn is a Lester building, that won’t be a problem. When we get an address for a renovation project, we can go into our archives to find out if it’s one of ours or not. If it’s ours, we can easily retrieve plans that are decades old.”
If you don’t have access to the original plans, some groundwork is required to determine the pole spacing to make sure the existing building can support the extra weight of your addition. Otherwise, the building could collapse, he warned.
Roof lines are another consideration. A customer recently hired Lester to double the warehouse space of their existing commercial building. “This project was unique in that we had to figure out how to add on to the side of the building, instead of the end, due to the slope of the roof,” Bjelland said. “Because we had the original plans, we were able to design a truss system that tied into the roof line they had.”
Finally, changing the use of a building has its own set of concerns. For example, if someone wants to turn a storage building to a commercial facility, they’ll need to work with their local municipalities to determine which building codes apply to the project and then comply with those regulations. Because commercial buildings house people instead of machines, like a storage building might, loading requirements will be more robust, Bjelland explained.
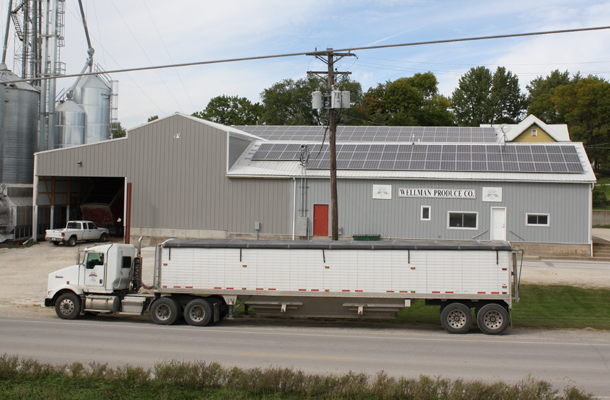
An existing feed mill and grain elevator with a 22' x 42' Lester lean-to addition and building remodel. (Project #219056)
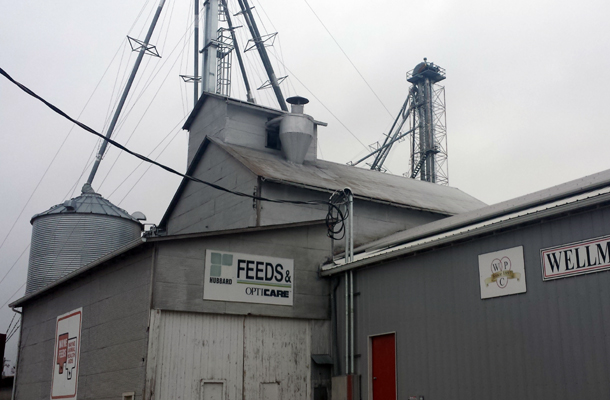
A before photo of the same project. This section of the original building was torn down and then a 22' x 42' Lester lean-to was added in its place. (Project #219056)
“Many older gothic barns have round roofs, which can be a challenge to tie new roof lines into,” Bjelland said. “Most also have post and beam construction that makes it difficult to verify the loading – they generally were never designed for or built to specific loads.”
Should an owner still want to add more space to their gothic barn, the safest work around is to add a structure to one end. “Lester did a building like that a couple years ago, where we added a 40 x 60-foot addition on to an old barn,” Bjelland said. “The new structure is entirely self-supported.”
If you’re planning an addition, research examples from contractors who have done projects similar to yours. “It’s good to have examples of similar alterations,” Bjelland said, “so that everyone understands the possible ramifications when altering the structure and how the resulting building will look and function. Sometimes, what a customer has in mind is not exactly the way the building will turn out in the end.”
Whether you’re looking for barn renovation ideas or have your project ready to go, Lester Buildings can help. Contact your local dealer or representative today.
When it’s time for a barn renovation, from re-siding and re-roofing to adding additional square footage like a lean-to or even an office or warehouse space, there are a few things owners should know before they get started. To help, we talked with two of Lester Building’s renovation experts, territory managers Ron Knapper and Joe Bjelland. Here’s their advice:
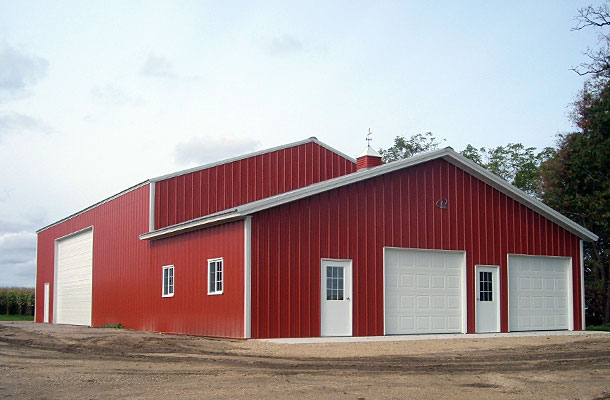
An exisiting Lester building with a shop addition. (Project #119363)
1. Get an expert opinion
Whether you’re reskinning a pole barn, replacing the roof or planning an addition, it’s always a good idea to bring a contracting expert to your site before starting a renovation project.“If you’re just replacing the steel siding, the initial consultation doesn’t have to be too involved,” Knapper explained. “But some customers want to reuse the existing steel, which makes sense economically. Unfortunately, it’s not always possible. If the steel is nailed on, it’ll be damaged when it’s taken off. If it’s screwed in, though, it will come off much cleaner and can be reused.”
Putting an addition on an existing structure is another story. “Make sure the renovation plans are reviewed by an engineer,” Bjelland said. “You need to understand what that building was initially designed for. If, for example, it was designed as an animal facility and the owner wants to turn it into a commercial building, that may or may not be possible based on the original plans.”
An engineer can also weigh in on whether a renovation will change snow drift loads on the roof, which can result in compromises to the building’s structural integrity. “Adding a taller addition to the end of a building could create an area on the roof of the existing building where snow accumulates,” Bjelland explained. “That snow drift load needs to be accounted for in renovation plans.”
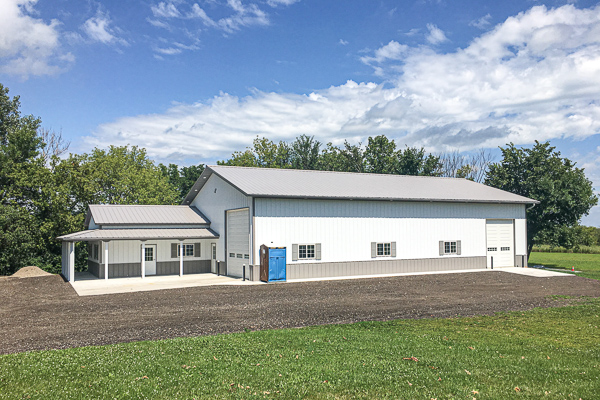
This insulated office addition to an exisiting Lester Building includes a wrap around porch. (Project #600760)
2. Plan for changing materials costs
Prices for steel, lumber and other construction materials fluctuate wildly in today’s market, thanks to global supply chain disruptions, many which stem from the COVID-19 pandemic. That’s why it’s a good idea to complete the design phase of your project and secure the necessary permits before seeking quotes from contractors.“It’s not uncommon today for a customer to be disappointed after they commit to a project and then apply for permits,” Bjelland said. “The permitting process can take a long time and, by the time they’re approved, the materials prices will have changed dramatically – sometimes to the point where the customer has to put the project on hold so they can reconfigure their budget. Having said that, though, post frame construction is still an economical way to go because it typically requires less lumber than a traditional stick built structure.”
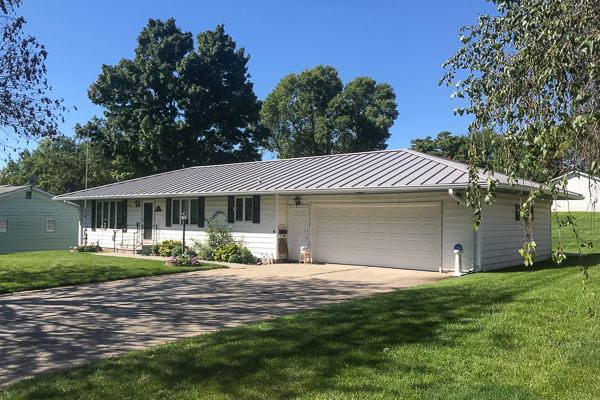
The Eclipse Roof System was used to re-roof this residential home. (Project #609624)
3. Be prepared for surprises
There are always surprises that come with alterations. Even a simple roof replacement can reveal leaks that caused rot in trusses and purlins over the years. Not only that, but customers are often surprised at the number of options available for replacement materials and the companies that install them. Increasingly, consumers are choosing the Eclipse Roof System for their durability and weathertightness.Reskinning can also reveal the unexpected – once the side panels are removed, you could discover that columns need replacing, too.
“Depending on the age of the building, you need to assess the condition of the columns,” Knapper said. “Periodically, a column will be rotted and we’ll have to stop what we’re doing, dig it out, and put in a new footing and column. I had a situation where the customer’s existing building was leaning well over a foot because the original builder didn’t put in the proper footings. Frost was getting to it and raising the structure. The only solution was to dig the columns out, put in bigger footings and reset the columns.”
The best way to prepare for unforeseen situations is to have a dedicated contingency budget. How much depends on the project, Bjelland said. “If you’re adding on to a building that has insulation and interior walls covering up the structure on the inside, you’re going to want more contingency money than if everything is open on the inside and you can clearly see the structure.”
4. Find the original blueprints
If you’re planning a barn renovation that includes adding on to the existing building, there are a host of structural factors that must be taken into consideration, so it’s important to try to obtain the plans for the existing building.“What type of renovation is possible depends on how the existing building was constructed,” Knapper said. “If your pole barn is a Lester building, that won’t be a problem. When we get an address for a renovation project, we can go into our archives to find out if it’s one of ours or not. If it’s ours, we can easily retrieve plans that are decades old.”
If you don’t have access to the original plans, some groundwork is required to determine the pole spacing to make sure the existing building can support the extra weight of your addition. Otherwise, the building could collapse, he warned.
Roof lines are another consideration. A customer recently hired Lester to double the warehouse space of their existing commercial building. “This project was unique in that we had to figure out how to add on to the side of the building, instead of the end, due to the slope of the roof,” Bjelland said. “Because we had the original plans, we were able to design a truss system that tied into the roof line they had.”
Finally, changing the use of a building has its own set of concerns. For example, if someone wants to turn a storage building to a commercial facility, they’ll need to work with their local municipalities to determine which building codes apply to the project and then comply with those regulations. Because commercial buildings house people instead of machines, like a storage building might, loading requirements will be more robust, Bjelland explained.
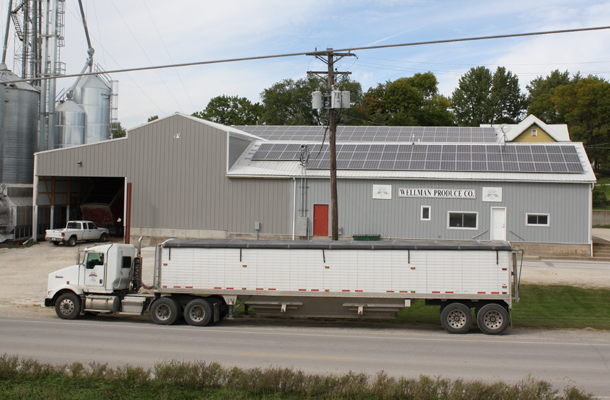
An existing feed mill and grain elevator with a 22' x 42' Lester lean-to addition and building remodel. (Project #219056)
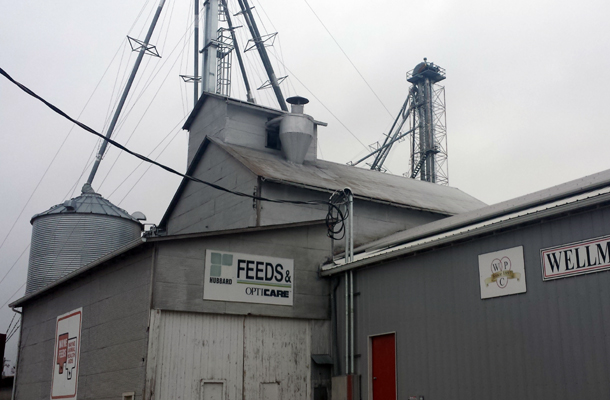
A before photo of the same project. This section of the original building was torn down and then a 22' x 42' Lester lean-to was added in its place. (Project #219056)
5. If you’re renovating an old barn
Renovating a pole barn is, generally, easier than updating an older gothic barn, primarily because it’s easier to determine a pole barn’s construction and loading.“Many older gothic barns have round roofs, which can be a challenge to tie new roof lines into,” Bjelland said. “Most also have post and beam construction that makes it difficult to verify the loading – they generally were never designed for or built to specific loads.”
Should an owner still want to add more space to their gothic barn, the safest work around is to add a structure to one end. “Lester did a building like that a couple years ago, where we added a 40 x 60-foot addition on to an old barn,” Bjelland said. “The new structure is entirely self-supported.”
6. Check out prospective contractors
Oftentimes, reroofing and reskinning projects in rural areas don’t require building permits. So, if a county or state inspector won’t be ensuring the integrity of the workmanship on your project, you need to know your builder’s reputation and don’t hesitate to ask them for references. To learn more about what to look for when searching for a building supplier, download a free copy of Evaluating your Building Supplier.If you’re planning an addition, research examples from contractors who have done projects similar to yours. “It’s good to have examples of similar alterations,” Bjelland said, “so that everyone understands the possible ramifications when altering the structure and how the resulting building will look and function. Sometimes, what a customer has in mind is not exactly the way the building will turn out in the end.”
Whether you’re looking for barn renovation ideas or have your project ready to go, Lester Buildings can help. Contact your local dealer or representative today.