From Pole Barns to Post Frame Construction
Barns – the iconic emblem of the American rural landscape. They’ve graced our geography since colonial days with all sorts of shapes, sizes and functions. They’ve also changed over time to meet the evolving needs of our hardworking farmers.
In celebrating Lester Building’s 75th anniversary, we thought we’d take a look at how one structure has not only advanced along with modernized agricultural practices, but also has, uniquely, found a place in town and the city.
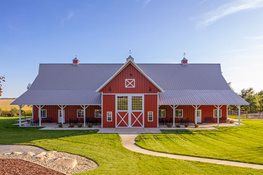
From pole barn to post frame construction
The traditional American pole barn is a product of the 1930s Great Depression. Farmers had little to no cash or credit but needed structures to protect their equipment and perhaps a few cows or a horse. So, they turned to old, round utility poles, which were inexpensive and readily available, to construct new buildings that were, essentially, small rectangles made by attaching trusses to the poles. Farmers of that era also used metal roof and sidewall sheeting to reduce construction costs even further.
As the country emerged from the second World War and the economy recovered, technology advanced farming practices and farm equipment began growing larger. The need for bigger structures to house more animals and bigger implements followed.
“The university extension services in the Upper Midwest began publishing DIY plans that farmers could use to fabricate trusses with gusset plates made out of plywood and glue,” said Paul Boor, VP of engineering and product development at Lester. “With these plans, farmers built some fairly substantive structures – up to 60-feet wide – but it was still pretty rough construction.”
Two subsequent innovations – the metal tooth truss plate and the laminated, engineered post – eventually moved pole barn production off the farm. Fabricating these components required specialized equipment that farmers didn’t have.
“That’s also the time when we stopped calling them pole barns and started using the term post frame construction,” said Lester Dealer Sales Manager Rick Sagness.
Agricultural buildings continued to evolve into the late 1980s and early 2000s as the industry leveraged technology to enhance the housing, care and welfare of dozens, and then hundreds – and even thousands – of animals, allowing farmers to specialize in just one kind of livestock. Some of the technology that plays a role in the design and manufacturing of today’s modern American pole barn includes automatic feed and waste disposal systems, milking carousels that accommodate hundreds of dairy cows at one time, and even robotics for heavy horse lifting at equestrian estates.
Along with their livestock peers, grain farmers also turned to specialization. Moving toward monoculture meant bigger harvests requiring larger equipment and the need for increased space to store both grain and machines. Technology that meets these needs today can heavily influence barn design. For example, “I’ve had farmers come up to me and say, ‘I don’t want my building to sweat on my million-dollar combine, what can we do?’ Here at Lester, we have multiple ventilation options for them to choose from,” Sagness said.
Moving into the commercial market
Just about anyone who’s been around the block a few times will remember the global recession of the early 1980s and the accompanying American farm crisis. Agriculture’s appetite for post frame construction suddenly diminished, and post frame builders who wanted to survive the economic downturn looked to enter other markets.
“People in town wanted to build buildings but didn’t have a lot of money,” Boor said. “Before [post frame builders] could step in, we had to learn more about design loads to meet the building codes for commercial structures in town.”
Boor was instrumental in developing a tool known as the Diaphragm and Frame Interaction Calculator (DAFI) with the University of Wisconsin that automated the calculations post frame builders needed to accurately design structures that met local building codes. “That was a huge deal because it allowed us to enter the commercial market,” he recalled.
“Commercial was the right fit,” Sagness added. “Take a look at mini malls in any area of the U.S., they’re not unalike the agricultural buildings we were manufacturing. So are warehousing and other commercial storage buildings. Today, Lester Buildings has constructed everything from the simple to the complex, including refrigerated warehouses and sports complexes to dental offices and fire stations.”
The pole barn comes home
Perhaps it was inevitable that the next frontier for post frame builders was the residential market. But why would anyone want to live in a pole barn?
Because, well, pole barn homes (also known as shouses, barndomiums and shomes) can be beautiful. “There are no limitations to what you can do on the inside because you don’t need load-bearing walls,” Sagness explained. “You can design the inside however you want.”
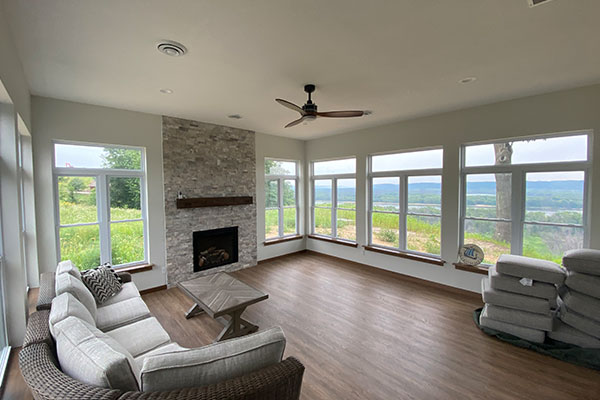
Project #614046
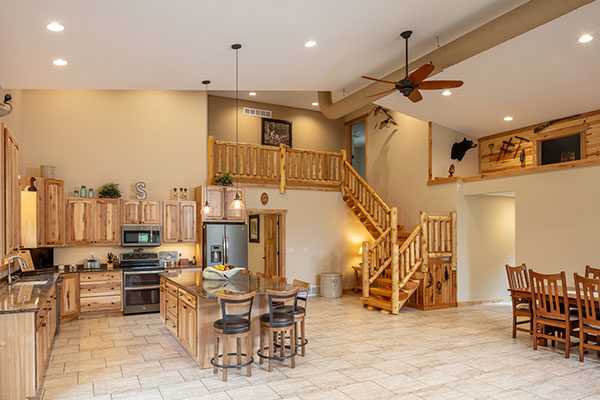
Project #514664
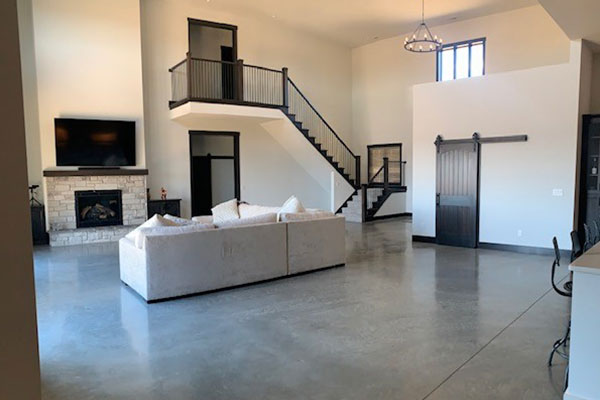
Project #614017
Throw in the advantages of speed and ease of construction, superior energy efficiency and durability compared to traditional residential construction, and less exterior maintenance, and it’s no wonder that the residential market is mushrooming.
Born out of necessity during a trying time in our country’s history, the American pole barn has truly come a long way from its humble agricultural beginnings. Today’s post frame buildings can be constructed to meet every consumer’s need and aesthetic preference. Contact us today to learn how Lester Buildings can help you create the building of your dreams.
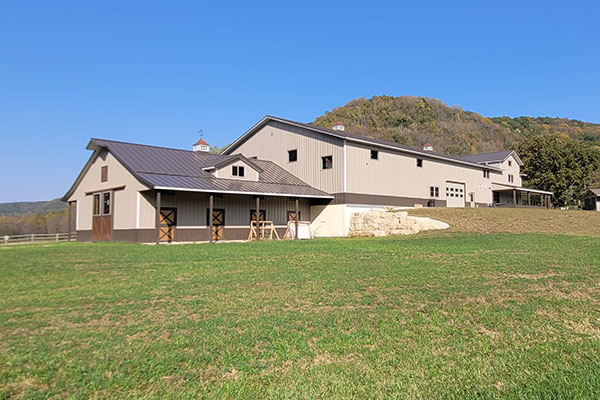
Project #613520